Automation in Order Picking
Order picking, the process of retrieving products from storage to fulfill customer orders, is the lifeblood of any warehouse operation. In the competitive landscape of modern logistics, mastering order picking is akin to perfecting a complex dance routine—precision, timing, and coordination are essential. In fact, order picking can account for approximately 55% of all warehouse activities, making it a focal point for efficiency improvements.
Given its significant impact on efficiency and customer satisfaction, optimizing order picking processes is a priority for many businesses. As the backbone of fulfillment operations, effective order picking ensures timely deliveries and maintains inventory accuracy, directly influencing a company's reputation and profitability.
The Marathon of Warehouse Workers
Ever wondered why warehouse workers have such enviable step counts? Warehouse workers often find themselves traversing vast distances during their shifts. It's common for an order picker to walk between 7 to 15 miles daily within the facility.
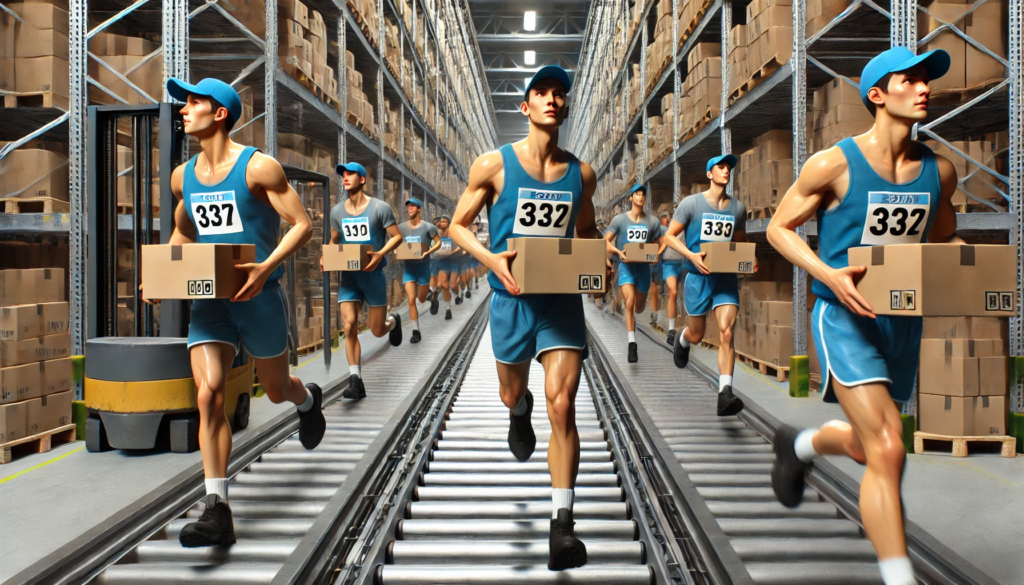
This extensive travel not only contributes to worker fatigue but also consumes a substantial portion of their working hours. In fact, walking and manually picking orders can account for more than 50% of the time associated with picking tasks. This inefficiency highlights the need for strategic warehouse layouts and the integration of automation technologies to reduce unnecessary movement. By minimizing travel distances, businesses can enhance productivity, reduce physical strain on workers, and streamline operations.
The Cost of Errors
"Measure twice, cut once"
Accuracy in order picking is crucial, yet even the most efficient warehouses are susceptible to mistakes. The industry average picking error rate hovers between 1% to 3%. While this percentage may seem minimal, the repercussions are significant. Errors in order fulfillment can lead to increased operational costs, returns processing, and, most critically, diminished customer satisfaction. In today's competitive market, where customers expect swift and accurate deliveries, maintaining high accuracy levels is paramount. Implementing technologies such as pick-to-light systems, RFID, and voice picking can reduce error rates by 67% compared to manual methods. As the saying goes, "Measure twice, cut once" emphasizing the importance of accuracy in operations.
Automation to the Rescue
Enter automation, the warehouse superhero. The integration of automation solutions in warehouses has revolutionized order picking processes. Automated Storage and Retrieval Systems (AS/RS) have the potential to increase order accuracy levels to above 99.99%. These systems minimize human error and enhance speed in retrieving items. For instance, Amazon's investment in robotics, including robotic arms like Robin and Sparrow, has significantly increased warehouse efficiency and is projected to save the company billions annually. Automation not only boosts accuracy but also reduces the physical demands on workers, allowing them to focus on more complex tasks. Additionally, automation can reduce warehouse operating costs by up to 30%. As technology advances, the role of automation in order picking continues to expand, offering solutions to longstanding challenges in warehouse management.
Speeding Things Up
In the realm of order fulfillment, speed is a critical factor. Implementing automation can increase picking speeds by up to 500%. Technologies such as conveyors and sorters reduce the time workers spend walking, allowing them to complete more picks per hour. For example, the average order picker can pick between 60 to 80 picks per hour, whereas with the aid of automation, this rate can soar to up to 300 picks per hour. This acceleration not only enhances productivity but also shortens order cycle times, enabling faster deliveries to customers. In a world where next-day or even same-day delivery has become the norm, increasing picking speed is essential for maintaining a competitive edge. Moreover, pick-to-light systems can improve pick rate productivity by 30-50%.
The ROI of Automation
Investing in automation technologies requires substantial capital; however, the return on investment (ROI) can be both significant and swift. Simple systems like Warehouse Management Systems (WMS) and pick-to-light can have a payback period ranging from 0.5 to two years. For instance, John Lewis implemented autonomous robots in its warehouse operations, resulting in a 75% increase in storage capacity and savings of £1 million. These improvements not only offset the initial investment but also lead to ongoing operational savings. Companies must conduct thorough cost-benefit analyses to determine the most effective automation solutions for their specific needs. As automation technologies become more accessible and affordable, even small to medium-sized enterprises can reap the benefits of increased efficiency and reduced labor costs.
Labor Shortages: A Pressing Concern
"Robots don't call in sick"
The logistics industry is grappling with significant labor shortages, with nearly 90% of warehouses reporting difficulties in finding and retaining quality labor. This scarcity is driven by factors such as an aging workforce, the physically demanding nature of the job, and competition from other sectors. The labor gap underscores the need for efficient order picking systems that can maintain productivity levels despite a reduced workforce. Automation emerges as a viable solution, alleviating the pressure on human resources by taking over repetitive and strenuous tasks. As one warehouse manager aptly put it, "Robots don't call in sick". By integrating automation, companies can mitigate the impacts of labor shortages, ensuring continuity and efficiency in their operations.
Safety First
Warehouses are inherently hazardous environments, with workers exposed to risks such as heavy lifting, collisions with machinery, slips and falls, and repetitive strain injuries. The numbers are alarming—every year, warehouse accidents cost businesses over $4.6 billion in direct and indirect expenses. Additionally, warehouse-related injuries result in thousands of lost workdays annually, significantly impacting productivity and increasing insurance premiums. One of the biggest contributors to workplace injuries in warehouses is manual handling and lifting. Studies show that 35% of all work-related injuries in logistics stem from overexertion, including strains and sprains due to improper lifting techniques. Another common cause of injuries is the high traffic of forklifts.
„The time to repair the roof is when the sun is shining”
Automation plays a crucial role in mitigating these risks. The implementation of Autonomous Mobile Robots (AMRs) can significantly reduce the number of worker injuries by eliminating the need for manual material handling and transportation. For example, Amazon’s Proteus and Sequoia robots are designed to move heavy items within warehouses while preventing human contact, reducing the chances of collisions.
Another safety-enhancing technology is wearable sensors and AI-powered monitoring systems. Some companies now equip workers with smart wearables that track posture, lifting techniques, and fatigue levels, alerting them in real-time to potential injury risks. Similarly, AI-driven computer vision systems can monitor warehouse floors for unsafe behaviors, such as improper stacking of items or blocked emergency exits, and provide automatic alerts to supervisors.
As John F. Kennedy once said: "The time to repair the roof is when the sun is shining". The best time to implement safety measures is before an accident occurs. By integrating automation, AI, and real-time monitoring, companies can reduce workplace injuries by up to 70%, lower insurance costs, and foster a safer, more productive work environment. In an industry where speed and efficiency are critical, ensuring worker safety is not just a legal and ethical responsibility—it’s also a smart business decision.
Space: The Final Frontier
In warehouses, every square metre is at a premium. Unfortunately, according to studies, up to 80% of warehouses are not fully optimised in terms of space utilisation. In practice, this means inefficient racking, wasted storage space and suboptimal picking paths. Aisles that are too wide, unnecessarily high spaces above products or unused height areas can drastically reduce warehouse efficiency.
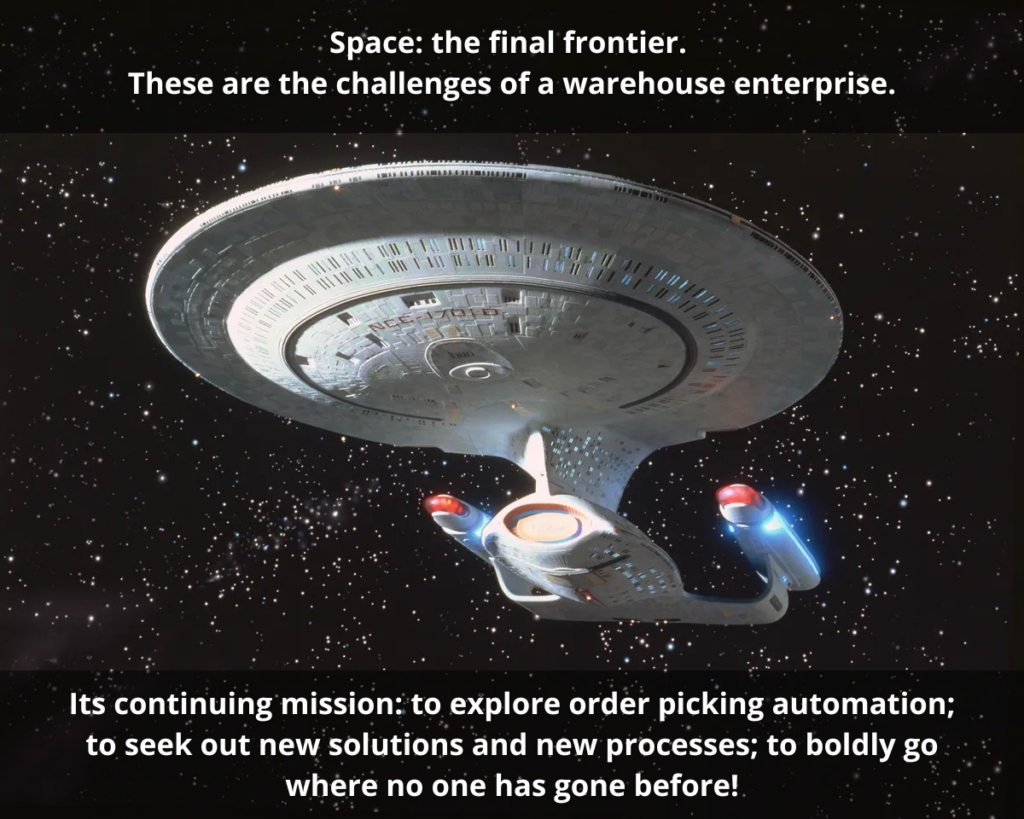
Modern technology makes it possible to solve this problem. Automated storage and retrieval systems (AS/RS) can increase warehouse capacity by up to 40%, allowing products to be stored in a more compact structure. In addition, the use of vertical storage, mobile robots and high-bay systems allows maximum space utilisation without the need to expand the building.
By implementing space analytics, WMS systems and rack utilisation monitoring technologies, companies can significantly improve warehouse efficiency. It is worth remembering that better space management not only increases storage capacity, but also speeds up order picking and reduces internal transport times. So, although, as Jean-Luc Picard used to say,
“Change always comes later than we think it should”
, it is important that it does come eventually.
The Future of Order Picking
The future of order picking is increasing automation, the use of artificial intelligence and the integration of IoT systems. Already, large companies such as Amazon, DHL and Walmart are extensively testing autonomous picking robots that can operate 24/7 and increase picking efficiency by up to 200-300%.
Artificial intelligence (AI) is increasingly being used to predict demand and optimise picking routes to reduce lead times and minimise errors. Intelligent systems can analyse historical data, seasonality of sales and current trends to predict which products are most likely to be ordered and adjust warehouse layout accordingly.
The next step is the full integration of ERP, WMS and MES systems, which will enable seamless management of the entire logistics process from order receipt to dispatch. In the future, we can expect to see an increasing proportion of goods-to-person systems, where products ‘come’ to the operator themselves, rather than forcing them to travel long distances in the warehouse.
Companies that fail to invest in modern solutions may lose competitiveness and fail to keep up with market leaders. With increasing customer expectations for speed of delivery and labour availability issues, the future of order picking is automation, AI and making the most of modern technology.
###
Article by: Marcin Maroszek
###
Sources:
https://www.logiwa.com/blog/warehouse-order-picking-methods
https://www.netsuite.com/portal/resource/articles/ecommerce/order-picking.shtml
https://www.conveyco.com/blog/improve-warehouse-efficiency-with-automation/
https://www.mhlnews.com/warehousing/article/22050881/a-12-step-journey-to-order-picking-perfection
https://www.mhlnews.com/transportation-distribution/article/22036127/getting-your-warehouse-in-order
https://www.connexxt.pl/ekspert-w-branzy/poradnikeksperta/czynniki-oplacalnosci-automatyzacji-magazynu.html?utm_source=chatgpt.com
https://www.logistyka.net.pl/bank-wiedzy/item/95290-logistyka-4-0-magazyny-na-sciezce-automatyzacji-i-robotyzacji
https://www.conveyco.com/blog/warehouse-automation-statistics/
https://www.grandviewresearch.com/press-release/global-warehouse-order-picking-market
https://www.scjunction.com/blog/6-warehousing-best-practices-for-your-supply-chain
https://www.amsfulfillment.com/12-order-picking-best-practices-for-maximum-efficiency/
https://www.zionmarketresearch.com/news/global-warehouse-order-picking-market
https://www.toyotamhs.com/blog/tips-for-effective-order-picking/
https://www.jomswsge.com/pdf-191201-113221?filename=Optimizing%20order%20picking.pdf
https://www.andersenmaterialhandling.com/material-handling-resources/warehouse-best-practices/
https://us.blog.kardex-remstar.com/order-picking-best-practices
https://www.businessinsider.com/amazon-warehouse-robots-picking-challenge-2025-2?IR=T
https://www.thetimes.com/business-money/technology/article/robots-help-john-lewis-stack-its-christmas-gifts-high-nl8x7rtlr
https://www.sstlift.com/blog/improve-warehouse-picking-speed-and-accuracy
https://www.tawi.com/insights/your-guide-to-efficient-order-picking/
https://www.rfgen.com/blog/efficiently-picking-your-way-to-success-best-practices-for-improving-order-picking-speed-and-accuracy-in-warehouse-management/